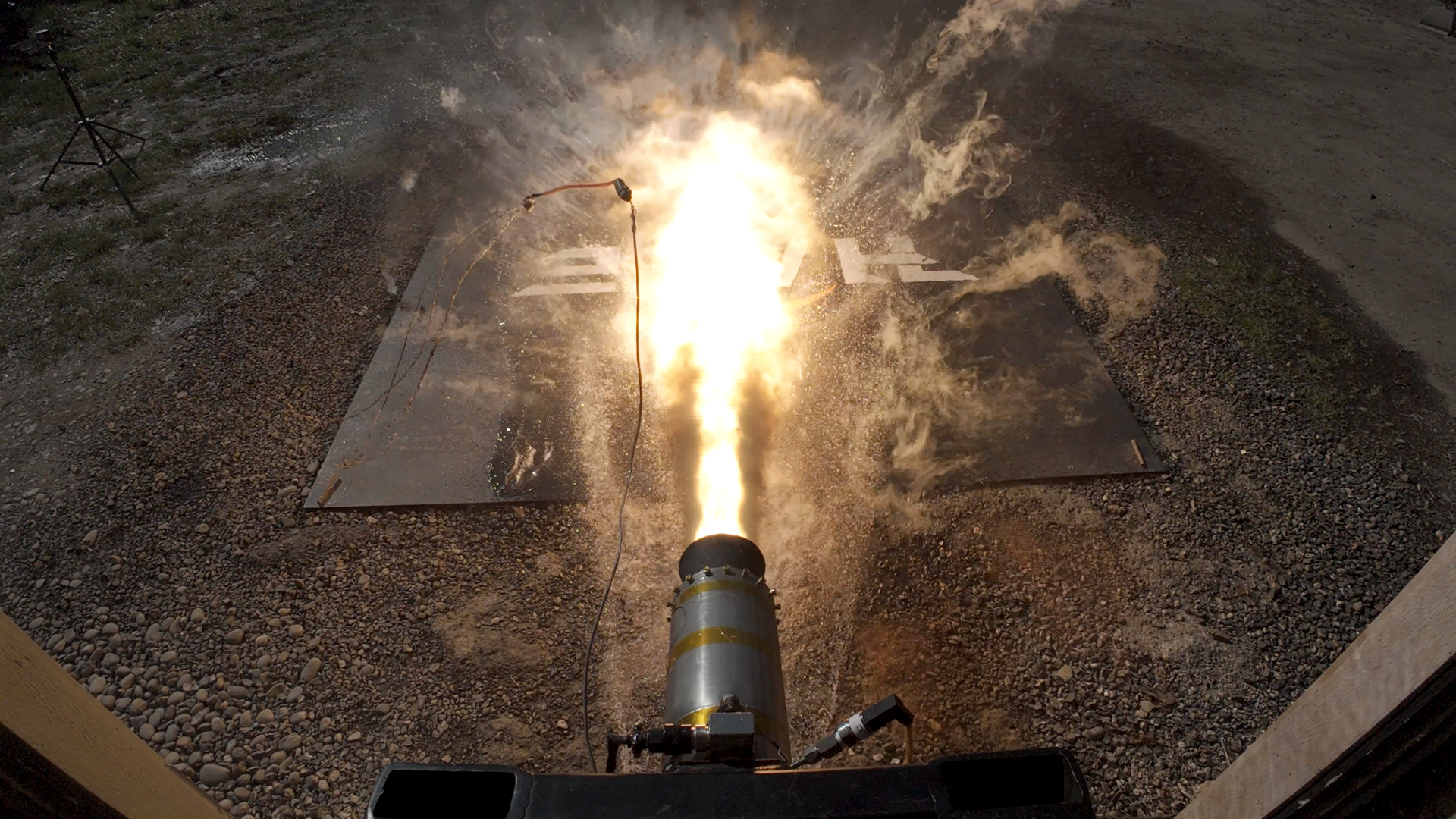
The High Altitude Liquid Engine (HALE) team is the creator of Oregon's most powerful liquid rocket engine. As one of six finalists in the Base 11 Space Challenge, we are working toward launching a single-stage liquid bipropellant rocket into space. The first collegiate team to achieve this goal will win a $1 million prize.
MIRA 2 HOTFIRE 1
On December 16th, the HALE team successfully conducted a static fire test of the Mira 2 engine, the most powerful liquid-fueled rocket engine ever built in Oregon. This summer, HALE plans to launch CETUS, a bipropellant kerosene-liquid oxygen rocket powered by the Mira 2 engine.
MIRA 2 HOTFIRE 2
On Feburary 28th, the HALE team successfully conducted the second static fire test of the Mira 2 engine. Following the first static fire of Mira 2 in December, the team implemented several key improvements in preparation for this attempt. Major updates include:
- Test stand upgrades, featuring enhanced sensor data collection and valve improvements.
- Integration of the new flight nozzle for more flight-representative performance.
- Refined standard operating procedures to streamline testing and improve safety.
Mira 2 produced 1681 pounds of thrust and validated the flight nozzle and its performance.
Stay up to date on our socials:
OUR ENGINES
Mira 1
We initially learned the finer details of handling liquid rocket engines through our first engine, Mira 1. This design is a pressure fed, Jet-A kerosene and liquid oxygen fueled engine with a pintle injector and ablative cooling. This engine had a peak thrust of 1,300 lbf and was Oregon's most powerful and first liquid rocket engine.
Mira 2
Mira 2, our second design, progresses on all lessons learned from Mira 1, and incorporates new technology. With a design thrust of 2,000 lbf, Mira 2 focuses on ease of manufacturing, assembly, and thermal longevity in a flight-weight design. On December 16th, Mira 2 was successfully static fired for the first time on HALE's horizontal test stand, Stellaris, with a thrust of 1,350 lbf. This test was conducted without the flight nozzle containing only a stub nozzle with no diverging section. Mira 2's second static fire was conducted on February 28th, further validating our design, flight nozzle, and test stand, producing 1681 pounds of thrust.
CETUS
Cetus is our sub scale launch vehicle designed to be a test bed for our full scale vehicle and plans to launch this summer. Cetus has full automation and repeatability, capable of launch multiple times a day. At 21 feet tall, Cetus is Oregon's largest rocket and has a target apogee of 37,000 ft.
Join Our Mailing List!
Join our mailing list here to receive updates on our current operations and more!
SUBTEAMS
HALE consists of six specialized subteams: Propulsion, Aero and Recovery, Structures, Fluids, Avionics, and Vertical Test Stand. Each subteam specializes on a distinct aspect of our subscale rocket, Cetus. While each group has its own area of expertise, all subteams collaborate closely and contribute towards the success of our team.
Propulsion
The Propulsion team focuses on the design, development, and testing of our liquid engines. This team works with our horizontal test stand, Stellaris, conducting testing to further develop and improve our propulsion capabilities.
Aero and Recovery
Aerodynamics & Recovery (A&R) is responsible for the design, manufacturing, testing, and implementation of the subscale flight vehicle recovery separation mechanism, avionics bay, parachutes, nose cone, fins, airframe, and sub-subscale test-flights. The development of the sub-subscale test rocket is a joint effort between the A&R and Avionics subteams, while the purchasing and integration of the airframe is a joint effort between the A&R and Structures subteams. All of these crucial components ensure the rocket’s smooth and stable ascent toward apogee and its controlled descent upon reaching the target altitude. Members are divided into subgroups to work on several components at once for maximum time efficiency, but are still required to collaborate and immerse themselves in each part of the process. Integration meetings with all of the other subteams on the flight vehicle are necessary to maintain awareness of weekly progress and ensure that A&R is meeting integration deadlines and the launch timeline.
Fluids
The goal of the Fluids subteam is to provide high-pressure nitrogen gas to the various systems of the launch vehicle, which in turn supplies liquid oxygen and kerosene to the engine. In a pressure-fed system such as the one HALE uses, compressed gas is used instead of a pump to push fuel and oxidizer to the engine. The onboard fluid delivery system will also be required to supply nitrogen gas to the Aero & Recovery subteam’s piston separation mechanism, the valve subteam’s pneumatically actuated ball valves, and a purge line that, upon activation, uses nitrogen to purge fuel and oxidizer from the engine and cease combustion. Other major components in the system include a pressure regulator for the pressurant (nitrogen) system that will be modified in-house to be electrically actuated and controlled, cavitating venturis that will create a stable mass flow rate to the engine, seven pressure transducer and 2 thermocouples to monitor the system, and various check and relief valves.
Avionics
The HALE Avionics sub-team is in charge of the electronics and software used to operate the flight vehicle and vertical test stand. The Avionics team creates PCBs used for prototyping and final products, manages rocket to ground communication, and is in charge of recording and transmitting all sensor data during flight. Most importantly, this team controls the deployment of the two parachutes that make up our recovery system.
Structures
The Structures team focuses heavily on manufacturing and collaboration on designs with other subteams. The team must design parts that are light and sufficiently strong, while also being fast and flexible to changes other subteams may require. This team requires clear communication, strong desire to learn new software, and the willingness to obtain many machine shop certifications.
VTS
The Vertical Test Stand (VTS) subteam is responsible for the design and manufacture of a mobile testing and launch platform capable of supporting both the subscale MIRA 2 flight vehicle and the eventual full scale flight vehicle. Once completed, the test stand will be capable of remotely fuelling and emptying the flight vehicle, holding the flight vehicle securely for vertical static testing, and functioning as a mobile launch platform. The key components of the VTS include the fluid systems (fuel, LOx, and pressurant), physical structures (supports, launch rail, etc.), the electronics for reading sensors and controlling valves, and the software capable of interpreting, storing, and displaying data as well as running automated control procedures. In the past two terms, fluids and structures have been the primary focus of the team with software and electronics being handled by the Avionics subteam.
THANK YOU TO OUR SPONSORS
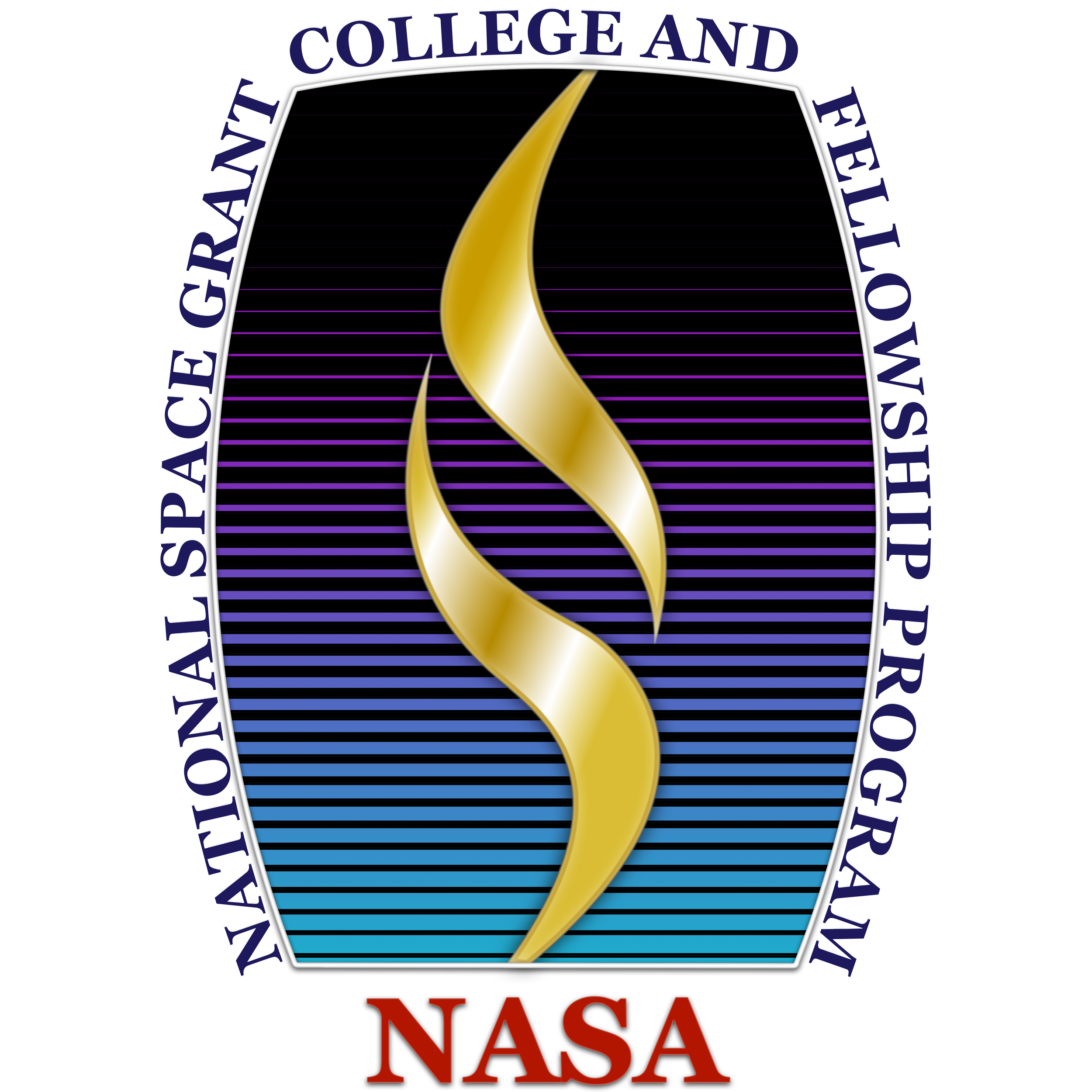
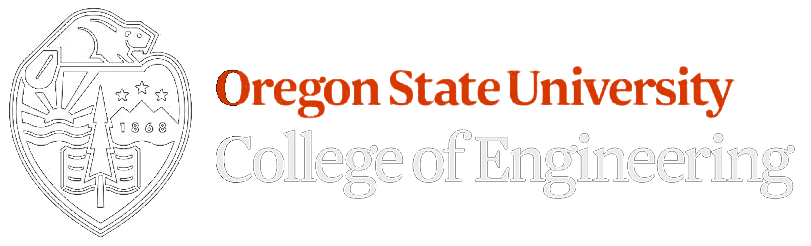
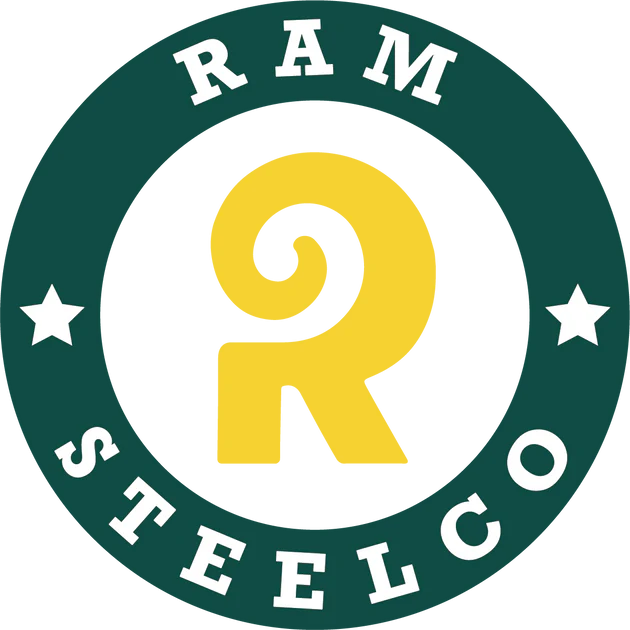

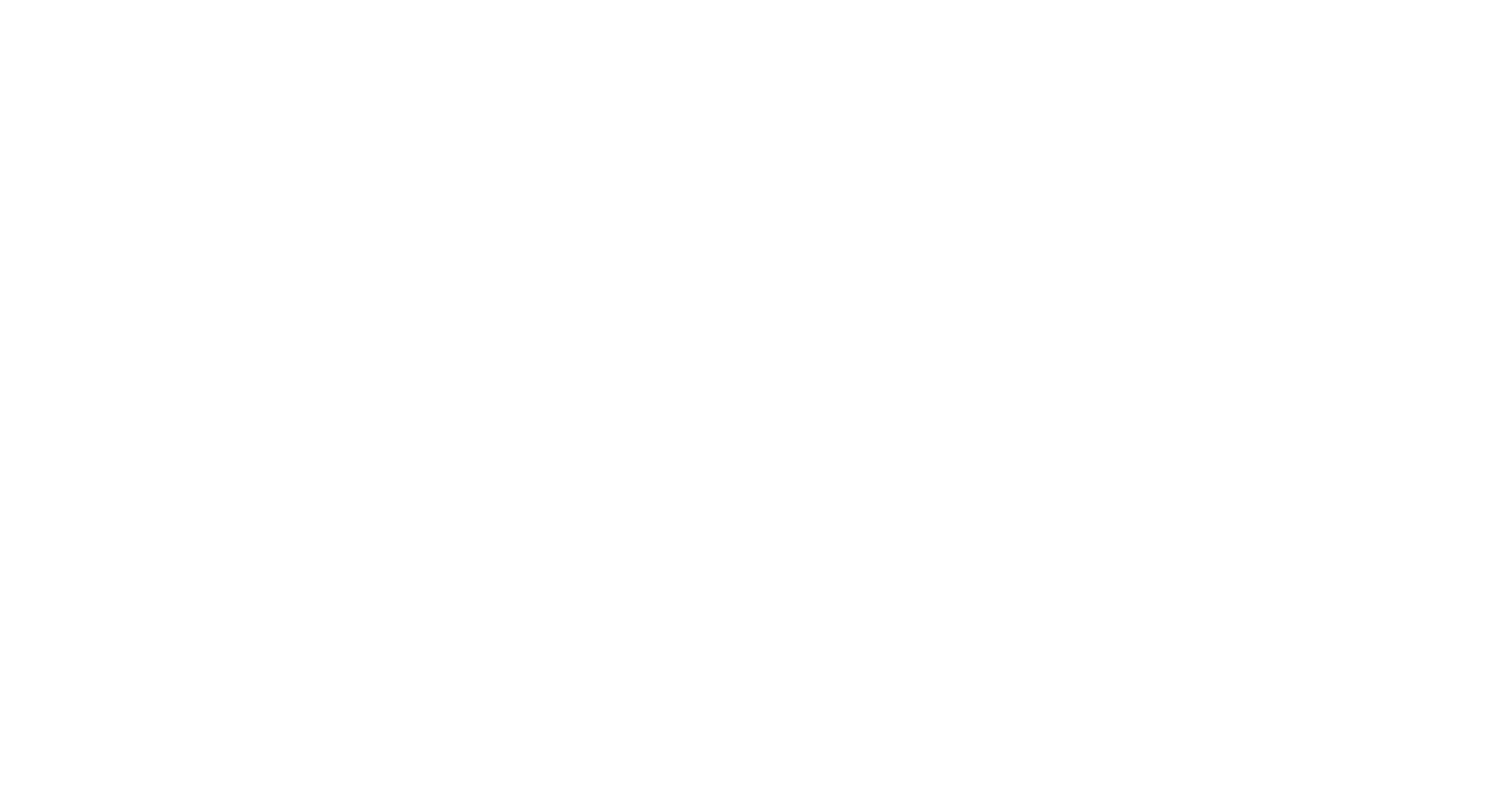
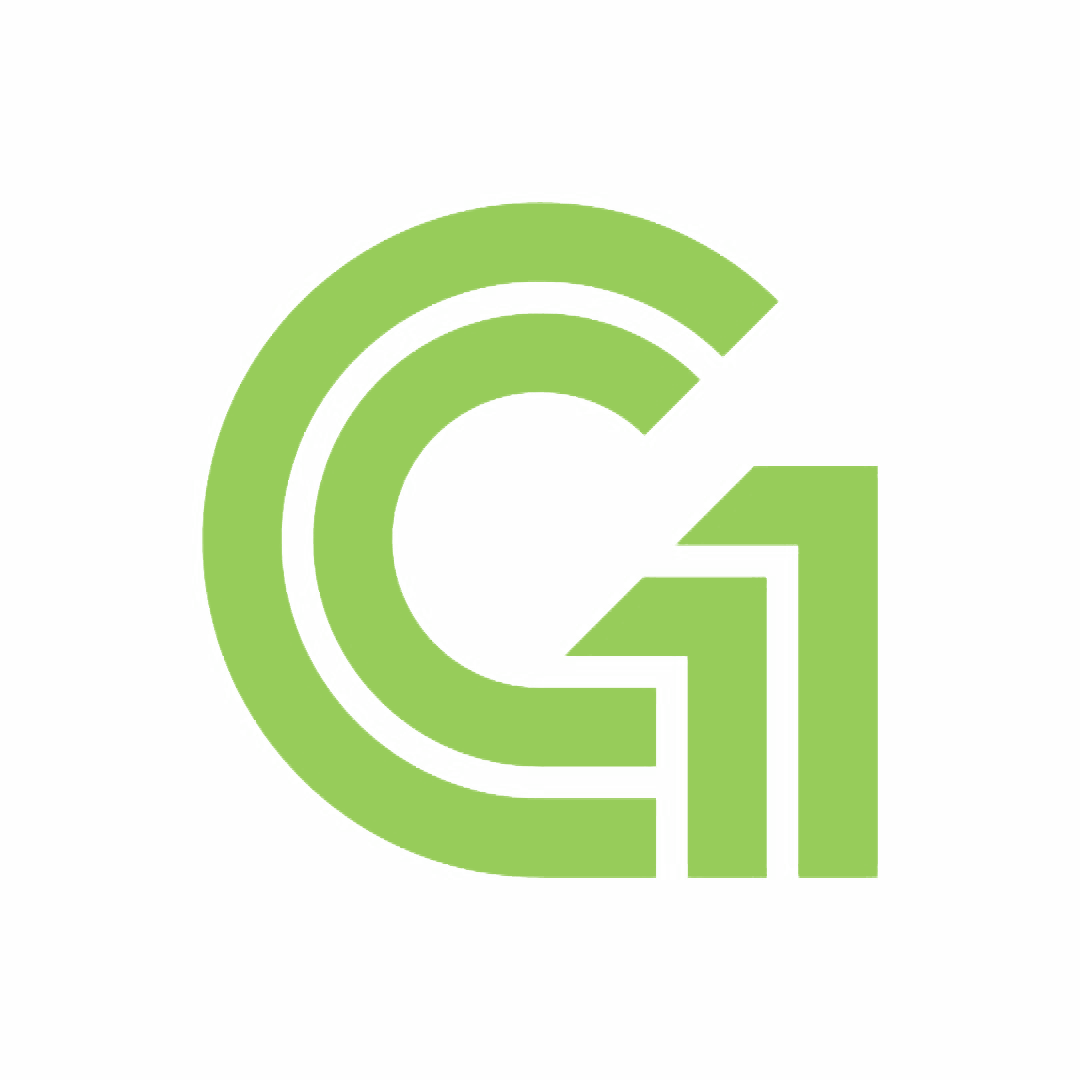

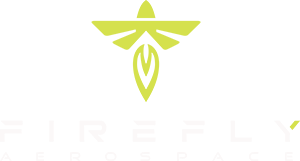
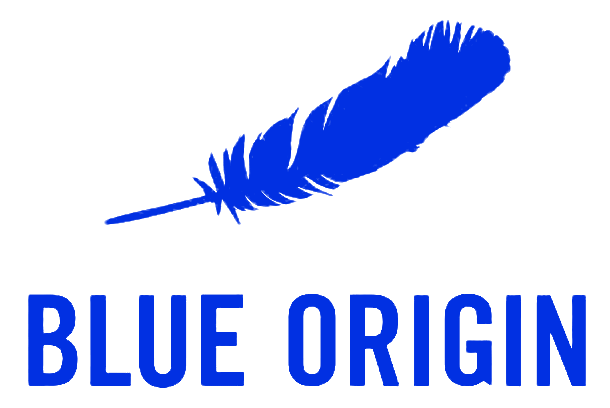
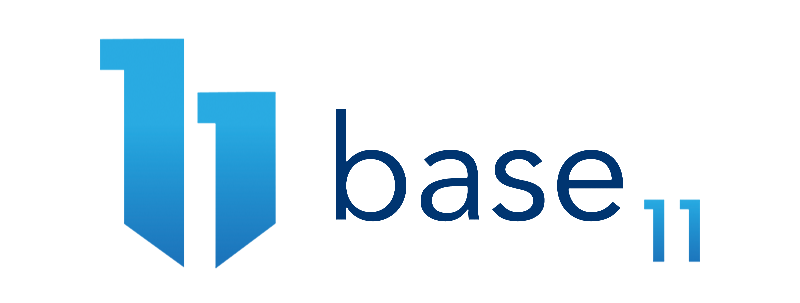
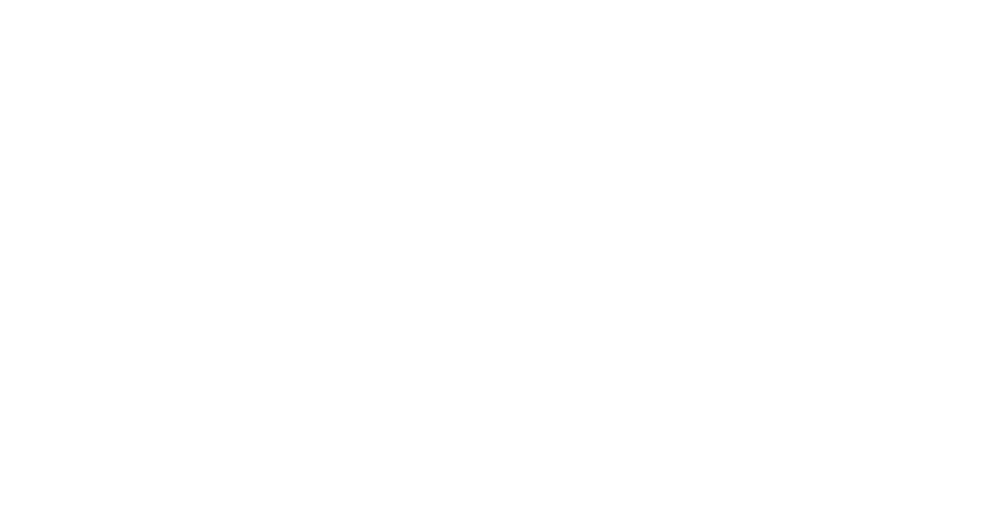

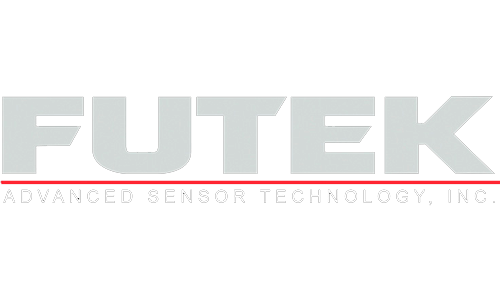
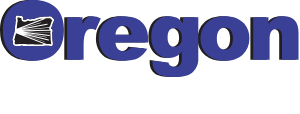
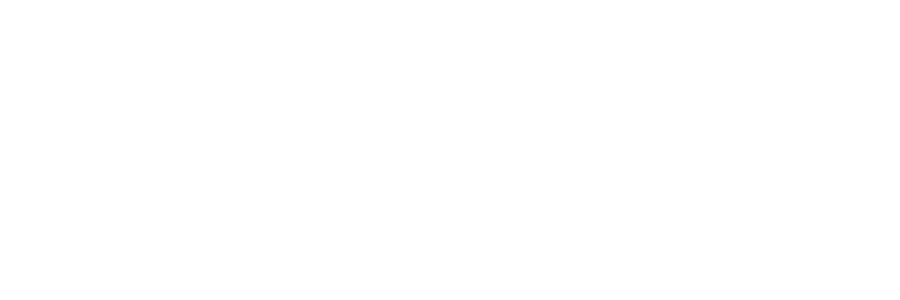

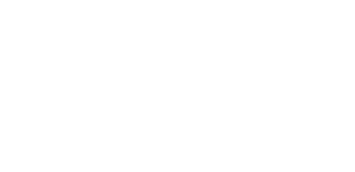

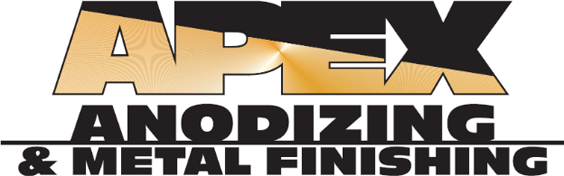
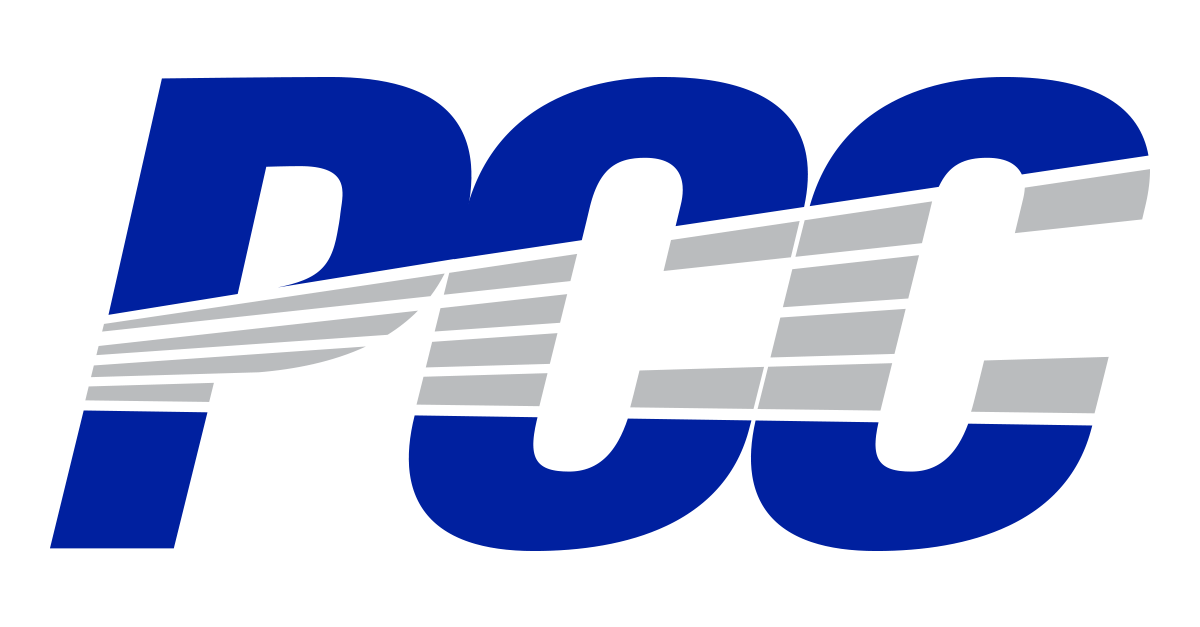
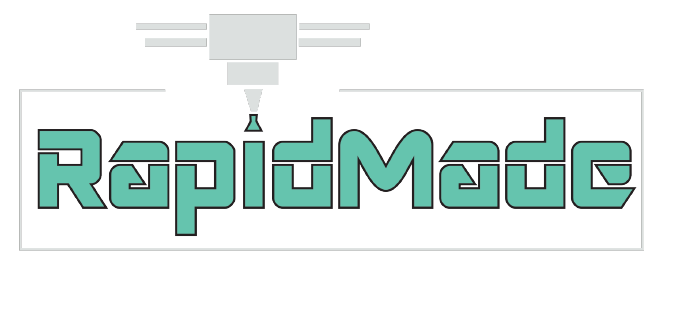
Stay up to date on our socials: